How sustainable is recycled polyester yarn?
rajeev • December 15, 2020
Recycled Polyester Yarn & Sustainability
Recycled Polyester Yarn or rPET is manufactured from used PET bottles & yarn waste which is then converted into chips, using environment-friendly recycling processes. In 2017, the organisation spearheading the international efforts in sustainable manufacturing in the textile industry - Textile Exchange - created an rPET Commitment to encourage brands and retailers to publicly commit to accelerating their use of recycled polyester by 25% by 2020. Many international brands including Gap, Ikea, H&M, etc. signed up to this commitment to increase their adoption of rPET by at least 25% by 2020.
This commitment has been tremendously successful. The aggregate target was reached two years early, in 2018, when the combined rPET use of the commitment signatories grew by 36%
The Impact:
To put this in perspective:
- 2,868,000,000 bottles diverted from landfill.
- 35,329,509 kg reduction in human toxicity.
- 1,849,464 MJ saved on primary energy demand.
- 122,823 kg reduced Co2.
The IKEA ambition is to not use any virgin oil based polyester in textiles by 2030. To commit to use 25% more rPET by 2020 is a natural step towards our ambition. We are committed to use resources with the utmost efficiency and turn waste into resources.
Lena Julle, IKEA Category Area Manager, Textiles
Recycled polyester, also known as rPET, is obtained by melting down existing plastic and re-spinning it into new polyester fiber. While much attention is given to rPET made from plastic bottles and containers thrown away by consumers, in reality polyethylene terephthalate can be recycled from both post-industrial and post-consumer input materials. But, just to give an example, five soda bottles yield enough fiber for one extra large T-shirt. This sounds like a great idea. But in reality, how sustainable is Recycled Polyester.
At Beekaylon, we are guided by three guiding principles to create products and inspire our production methodologies.
- Eliminate waste and pollution
- Keep products in use
- Regenerate natural systems
Let us look at what Textile Exchange (TE) has to say about this. According to TE,
- Using more rPET reduces our dependence on fossil fuels as the source of our fabrics. With the world shifting away from fossil fuels in all walks of life, this is ultimately a good thing
- Diverting PET bottles reduces the need to send them to landfills and thus reduces soil contamination, air & water pollution
- The production process also requires less energy consumption compared to virgin polyester
- Garments created from rPET do not degrade in quality and minimizes wastage. This could potentially become a closed loop system
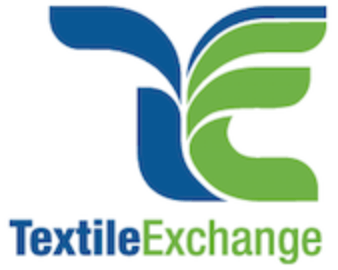
#1 - rPET prevents prevents plastic from the oceans
The NGO Ocean Conservancy estimates that over 8 million metric tonnes of plastic enter the ocean every year adding to the 150 million metric tonnes already circulating in the waters, thereby contaminating the marine ecosystems around the world. If this continues, by 2050 there will be more plastic in the ocean than there is fish!
Over 60% of seabirds and 100% of all sea turtles have plastic ingested inside them as they mistake plastic for food.
#2 - rPET is durable in quality and takes less energy to make
According to a 2017 study by the Swiss Federal Environment Agency, rPET’s production helps to reduce CO2 emissions by 32 percent in comparison to regular polyester. Converting PET into recycled polyester uses less water and energy than it would to produce virgin polyester. Most studies show that between 33-53% less energy is used to create recycled polyester vs virgin polyester. In addition, less CO2 emissions are produced and we do not need to use non-renewable resources (petroleum). We process recycled polyester yarns by extruding recycled chips. The recycled yarns are supplied to textile and floor covering manufacturers. This contributes to reducing our carbon footprint by reusing and recycling PET based products.
According to a 2017 study by the Swiss Federal Environment Agency, rPET’s production helps to reduce CO2 emissions by 32 percent in comparison to regular polyester. Converting PET into recycled polyester uses less water and energy than it would to produce virgin polyester. Most studies show that between 33-53% less energy is used to create recycled polyester vs virgin polyester. In addition, less CO2 emissions are produced and we do not need to use non-renewable resources (petroleum). We process recycled polyester yarns by extruding recycled chips. The recycled yarns are supplied to textile and floor covering manufacturers. This contributes to reducing our carbon footprint by reusing and recycling PET based products.
But more needs to be done
Though rPET takes 59% less energy to produce, it still requires more energy to produce when compared to natural products such as hemp or wool. (source - Stockholm Environment Institute)
We cannot afford to get the foot of the pedal and continue to look at reducing the energy consumption in producing recycled polyester yarn. We need to promote the use of products like
Poly-Go-Round
by more brands in the marketplace.
Needless to say, converting plastic waste into a usable product and preventing it from reaching landfills or the ocean is critically important. Adopting sustainable manufacturing practices and increasing the adoption of recycled polyester yarn in textiles and floor covering products is important for us at Beekaylon Synthetics.
With 49% of the global fiber production, polyester is the most widely used fiber in the apparel sector: more than 63,000 million tonnes of polyester fiber are produced annually. With that as a background Poly-Go-Round is crucial to our plans to develop a sustainable future for our planet.
There are more challenges to overcome and we need to promote the acceptance of recycled polyester yarns amongst brands. Which is crucial for a sustainable future for our planet.
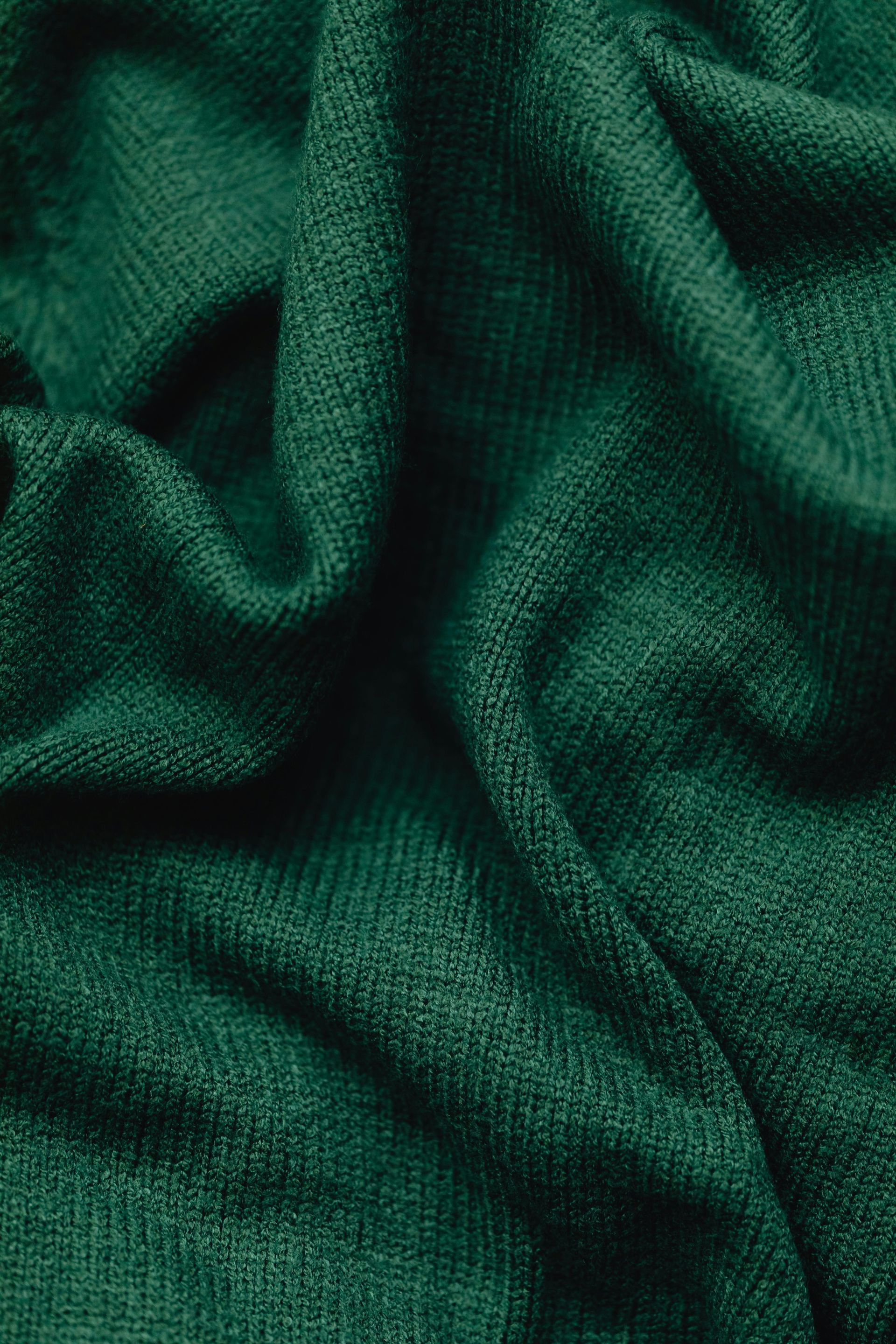
Polyester yarn has evolved significantly, overcoming misconceptions and proving its value in the textile industry. With continuous advancements in technology and sustainability, polyester remains a reliable, durable, and eco-friendly choice for modern textiles. Companies like Beekaylon are leading the charge in making polyester more sustainable and versatile, ensuring a greener future for the industry.
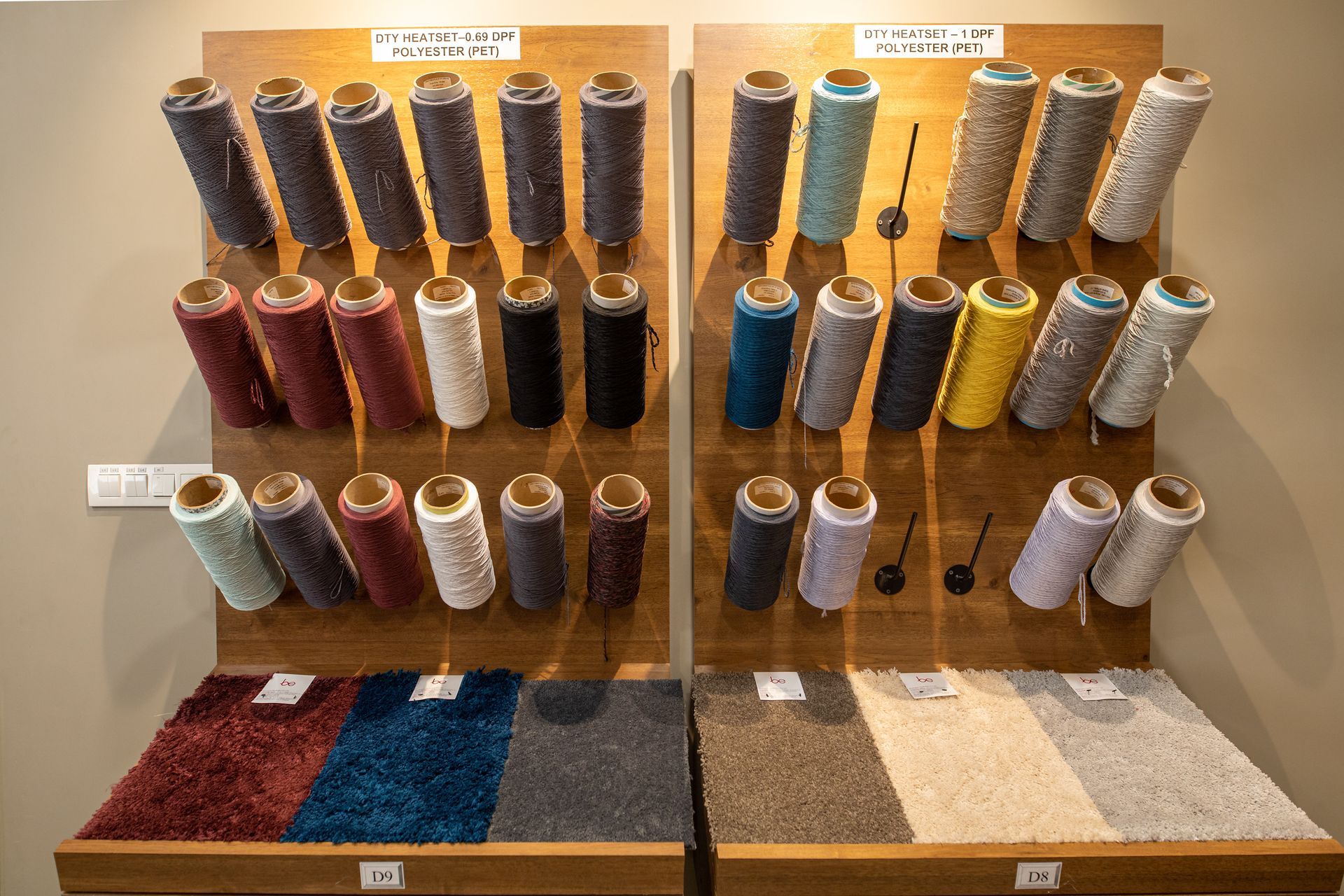
The textile industry is a constantly evolving sector that balances the art of innovation with the demands of functionality and sustainability. Among its many offerings, Bulk Continuous Filament (BCF) yarn stands out as a versatile and essential material, particularly in the carpeting and flooring segments.

The textile industry is at the cusp of a digital revolution, with AI, machine learning, and advanced digital tools transforming how we approach textile design. These innovations are not only enhancing creativity but also optimizing processes to create efficient, personalized, and sustainable solutions for the modern market.